1 Попередньо визначаємо величину розширення
,
де
– діаметр прошивня;
= 1,05 – 1,15 – коефіцієнт, що враховує втрати на вигар та видру.
2 Визначимо початкову висоту (ширину) заготовки:
.
3 Уточнюємо діаметр прошивня за формулою
.
4 Знаходимо діаметр оправки:
.
5 Знаходимо об'єм видри (рис. 20):
,
де h2 - 150 мм – висота перемички (бурту) видри;
h3 – висота стрижня видри;
Нзаг = В0;
hв = h2 + h3 = 1,1 Нзаг; h3 = 1,1 Нзаг – h2;
dв – діаметр внутрішній порожнистого прошивня;
Dв – діаметр зовнішній робочого прошивня.
Вибираємо параметри порожнистого прошивня за таблицею 32 відповідно до dпр.
Рисунок 20 - До визначення об'єму видри при прошивці порожнистим
прошивнем
|
Таблиця 32 - Основні розміри порожнистих прошивнів, мм
6 Визначаємо об'єм заготовки:
, де Ку = 1,03 – коефіцієнт вигару металу.
7 Розміри заготовки при вирубуванні зі злитка:
;
;
;
де n = 1,25… 2,5.
8 Визначаємо геометричні параметри заготовки.
Діаметр осадженої заготовки
.
9 Товщина стінки заготовки після осадки та прошивки:
.
10 Величина обтиснення стінки заготовки при розкочуванні:
.
11 Ступінь деформації за товщиною стінки:
.
12 Середня товщина стінки за весь процес розкочування:
.
13 Коефіцієнт формозміни:
,
тут "+" при
£ 1;
"-" при
³ 1.
14 Уточнюємо величину розширення:
.
15 Визначаємо остаточні розміри заготовки після осадки та прошивки:
.
Якщо
, то беруть +5;
якщо
, то беруть –5.
16Визначаємо масу нековальських відходів у відсотках.
Маса злитка розраховується:
,
де Мсл – маса злитка;
Мп – маса поковки з урахуванням напусків I і II роду, а також технологічних проб, державок на захват;
Мвідх – маса ковальських відходів (кінцеві обрубки, видра, обсічки);
Мпр – маса відходів із прибутком злитка;
Мпд – маса відходу з донною частиною злитка;
Муг – маса відходу на вигар.
Маса нековальських відходів(у відсотках):
Кно = 100 (Мпр + Мпд + Муг)/Мсл.
Звичайно масу нековальських відходів із звичайних злитків можна брати:
Мпр = (19,5…21,0) %;
Мпд = (3,5…4,5) %;
Муг = 3% (одне нагрівання);
Муг = 4,5% (два нагрівання);
Муг = 6% (три нагрівання);
Муг = 7,5% (чотири нагрівання).
Припустимий коефіцієнт виходу придатного металу злитка Квг = 100 – Кно.
17Маса злитка
,
де
;
- маса видри.
18 За таблицею 33 вибираємо параметри злитка, поданого на рисунку 21.
Рисунок 21 – Злиток
Таблиця 33 - Характеристика і розміри деяких обкатаних злитків,
використовуваних АТ НКМЗ
Маса
злитка Мзлит,
кг
| Розміри, мм
|
обкатаного злитка
| цапфи
|
D
| L
| d
| l
|
|
|
|
|
|
|
|
|
|
|
|
|
|
|
|
|
|
|
|
|
|
|
|
|
|
|
|
|
|
|
|
|
|
|
|
|
|
|
|
|
|
|
|
|
|
19 Перевіряємо за виходом придатного
Квп = 100 Мп/Мслт.
20 За таблицею 34 перевіряємо коефіцієнт виходу придатного металу для поковок (рис. 22), який не повинен бути більше значень, зазначених у таблиці 34.
Таблиця 34 - Припустимий вихід придатного для деяких
поковок АТ НКМЗ
Поковки
| Сталь
| Маса злитка, т
|
до 5 т,
подовж.
| до 5 т,
норм.
| 6…30
| 31…109
|
Вали
| Вуглецева
|
|
| 69,5
|
|
Плити
| Легована
|
|
| 68,8
|
|
Кільця
| Високолегована
|
|
| 67,5
|
|
а – вал; б – плита; в – кільце
Рисунок 22 -Види поковок АТ НКМЗ
21 Визначаємо інші витратні коефіцієнти:
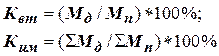
22 Перевіряємо умови. Якщо діаметр злитка D менше діаметра витратної заготовки Dзаг, то необхідно перерахувати довжину заготовки.
23 За відомим діаметром обкатаного злитка D визначаємо довжину заготовки:
,
де Dб = D.
24 Уявимо схему злитка після обкатки (рис. 23).
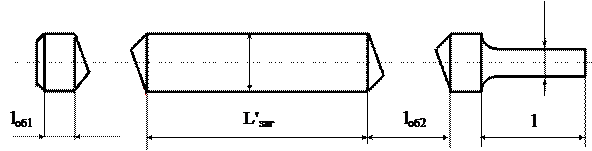
Рисунок 23 – Схема розкрою злитка після обкатки
25
Складаємо баланс металу (див. cамостійну роботу 14, пп. 23…30).