Гетерогенними називаються реакції, в яких реагуючі речовини перебувають у різних фазах, тобто сама реакція проходить на межі розподілу фаз.
Прикладом гетерогенної реакції є реакція розчинення речовини А у речовині В :
А(тв) + В(p)
АВ (р-р).
Ця реакція проходить на межі поділу фаз А (тв) - розчин.
У загальному випадку гетерогенна реакція - це послідовність п’яти стадій (см. рис.), кожна з яких має свої особливості:
I - доставка речовини з глибини фази на поверхню поділу;
ІІ - адсорбція вихідних речовин на поверхні поділу;
ІІІ - власне хімічна реакція на поверхні поділу;
ІV - десорбція продуктів реакції з поверхні поділу;
V - відведення продуктів реакції із зони реакції углиб фази.
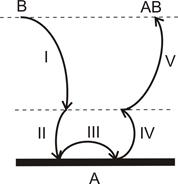
Схема гетерогенної реакції
Транспорт реагуючих речовин може здійснюватися конвекцією або дифузією. Конвекцією називають переміщення всього середовища в цілому. Конвекція розчину на границі з твердою поверхнею може відбуватися внаслідок переміщення твердого тіла або, частіше всього, через переміщення розчину.
Дифузією називається переміщення молекул речовини у нерухомому середовищі під дією градієнта концентрацій.
Розрізняють дифузію лінійну та просторову, нескінченну та обмежену, стаціонарну та нестаціонарну. Лінійна дифузія відбувається в одному напрямку, просторова - у різних напрямках. Дифузія називається нескінченною , якщо фронт дифузії у процесі гетерогенної реакції не встигає досягнути границі системи; дифузія є обмеженою, якщо фронт досягає границі системи. Під фронтом дифузії розуміють границю всередині розчину, де ще не помітні зміни концентрації, які спричинені процесом дифузії. При стаціонарній дифузії концентрація речовини в будь-якій заданій точці простору не змінюється з часом; при нестаціонарній - змінюється.
Гетерогенні процеси, як правило, здійснюються у перемішуваних розчинах, тобто доставка речовини до поверхні розподілу здійснюється шляхом конвекції. Однак, згідно з законами гідродинаміки, потік рідини поблизу поверхні твердого тіла уповільнюється, причому шар рідини молекулярних розмірів, безпосередньо прилеглий до поверхні, міцно утримується на ній. Це так званий дифузійний шар товщиною d, крізь який доставлення речовини до поверхні здійснюється тільки за рахунок дифузії. Всередині шару конвекція відсутня. Концентрація речовини у дифузійному шарі на границі з розчином дорівнює концентрації c0 в об’ємі розчину, а всередині дифузійного шару концентрація речовини зменшується до величини cs (рис. 12.2). Товщина дифузійного шару не є константою, а залежить від багатьох величин: щільності, в’язкості розчину, швидкості розчину, швидкості перемішування розчину.
Нехай швидкість стаціонарної дифузії і швидкість реакції на по верхні однакові. Нехай реакція на поверхні є реакцією першого порядку. Тоді для швидкості реакції W маємо
W = kcs 
де k - константа швидкості реакції першого порядку, b - константа швидкості дифузії.
Більшість твердофазних реакцій відносять до класу топохімічних. Топохімічною реакцією називається гетерогенна реакція, в якій бере участь хоча б одна тверда речовина і отримується хоча б один твердий продукт. Прикладами топохімічних реакцій є відновлення диоксиду германію воднем при отриманні напівпровідникового германію
GeO2(т) + 2Н2О(г) --> Ge(т) + 2Н2О(г),
термічне розкладання карбонату кальцію
СаСО3(т) --> СаО(т) + СО2(г).
Топохімічні реакції характеризуються специфічними кінетичними закономірностями. На початку топохімічної реакції швидкість її невелика (індукційний період), потім вона зростає, проходить через максимум та знижується практично до нуля. Ступінь перетворення при цьому звичайно змінюється за S - подібною кривою. Такий характер кінетичних закономірностей можна пояснити таким чином. У міру того як утворюються зародки фази твердого продукту реакції, з’являється реакційна поверхня поділу фаз, яка зростає у часі як внаслідок зростання зародків, що є, так і внаслідок утворення нових зародків.
Відповідно до цього швидкість реакції на початку процесу мала, а потім зростає. З розвитком поверхні поділу фаз зростаючі зародки продукту починають зливатися. Внаслідок відсутності вільної поверхні утворення нових зародків практично не відбувається. Тому площа реакційної поверхні поділу твердих фаз і відповідно швидкість реакції проходять через максимум. У подальшому злиття зародків приводить до зменшення реакційної поверхні та утворення суцільного шару твердого продукту, границя якого поступово просувається в глибину зерна вихідної твердої речовини. При цьому швидкість реакції поступово спадає до нуля.
Каталізом називається змінювання швидкості хімічних реакцій за наявності речовин, які називаються каталізаторами, які , беручи участь у процесі, самі наприкінці реакції залишаються хімічно незмінними.
Каталітичні реакції дуже різноманітні, однак до цих пір не існує загальної теорії каталізу. Зазначимо деякі загальні властивості каталітичних реакцій:
1 Дія каталізатора на реакцію не відбивається на її стехіометричному рівнянні. Однак у першому наближенні швидкість реакції прямо пропорційна кількості каталізатора.
2 Каталізатор не зміщує хімічної рівноваги. Якщо реакція оборотна, то каталізатор рівною мірою змінює швидкість прямої та оборотної реакцій.
3 Каталізатор має специфічність дії. Він може змінювати швидкість однієї реакції та не впливати на швидкість іншої.
4 Деякі речовини (не каталізатори) посилюють дію каталізатора, інші - послаблюють. Такі речовини називаються промоторами та ядрами.
За наявності каталізатора реакція прискорюється, тобто збільшується константа швидкості реакції:
k = Z × e-Ea/RT× eSa/R.
Таким чином, каталізатор збільшує швидкість реакції за рахунок зменшення енергії активації Еа або збільшення ентропії активації Sa .
Ключові терміни
Гетерогенни процеси; конвекція; дифузія; рівняння Фіка; топохімічні реакції; каталіз.
Питання для самоперевірки
1. Познайомтесь Дайте визначення гетерогенної реакції.
- Намалюйте загальну схему гетерогенної реакції і виділіть її основні стадії.
- Дайте визначення дифузії. Проведіть класифікацію дифузійних процесів.
- Напишіть рівняння Фіка і охарактеризуйте величини, що входять в ці рівняння.
- Розгляньте кінетику гетерогенної реакції при стаціонарної лінійної дифузії.
- Познайомтесь з основними висновками теорії, що описує перебіг реакцій при нестаціонарної лінійної дифузії.
- Які реакції називаються «топохімічними»? Опишіть основні особливості кінетики таких реакцій.
- Дайте визначення поняттю «каталіз». Перелічіть загальні властивості каталітичних реакцій.
- Визначте гомогенний і гетерогенний каталіз. Наведіть приклади.
- Назвіть причини впливу каталізаторів на швидкість хімічних реакцій.
Лекція 7. Стан умов праці у галузі
Аналіз умов праці у галузі за показниками шкідливості та небезпечності факторів виробничого середовища, важкості та напруженості трудового процесу в галузі.
1.Литейное производство. Появление опасных и вредных факторов возможно на всех стадиях обработки материалов при проведении технологического процесса в литейных цехах. Основными из них являются:
1) Пыль дезинтеграции и конденсации. Пыль литейных цехов по дисперсному составу относится к мелкой и мельчайшей фракциям. Особую опасность представляет пыль с размерами частиц 1-10 мкм. Количество пылинок с размером 2 мкм при разных процессах составляет 62 – 87 % общего числа пылинок, находящихся в воздухе. При очистке отливок в барабанах в выделениях пыли содержится до 95 % двуокиси кремния (песок), а при выбивке отливок – до 99 %, а кроме песка в пыли содержатся и другие фиброгенные компоненты, такие как уголь, окислы железа и других металлов. Экспериментальные исследования показали, что примеси аморфного углерода и железистых материалов в пыли усиливают ее вредное воздействие на человека.
2) Выделения паров и газов. Выделяются следующие пары и газы – это ацетон, ацетилен, бензол, окись азота, окись углерода, двуокись серы, углекислый газ, формальдегид, хлор и другие. Основной вредный производственный фактор – окись углерода (угарный газ), источники выделения – плавильные агрегаты, сушильные печи, агрегаты поверхностной подсушки форм.
3) Избыточное выделение теплоты. Интенсивность теплового потока на ряде рабочих мест достигает высоких значений. Известно, что интенсивность менее 0,7 кВт/м2 не вызывает неприятного ощущения, если действует в течение нескольких минут, а свыше 3,5 кВт/м2 уже через 2 секунды вызывает жжение.
4) Повышенный уровень шума. Наибольшие уровни шума характерны для участков формовки, выбивки отливок, зачистки, обрубки и др. ультразвук применяют для обработки жидких расплавов и очистки отливок. Источники ионизирующих излучений применяют для плавки и выявления дефектов в отливках.
5) Повышенный уровень вибрации. Источником общей вибрации является сотрясение пола и др. конструктивных элементов здания от ударного действия выбивных решеток, центробежных и др. машин; а источником локальной вибрации – пневматические рубильные молотки, трамбовки и др. Параметры общей и локальной вибрации регламентируются ГОСТ-12.1.012-78.
6) Повышенное напряжение в электрических сетях. Основные источники поражения электрическим током – электропечи, машины и механизмы с электроприводом (конвейеры, подъемно-транспортные устройства).
7) Наличие движущихся механизмов и машин.
2. Кузнечно-прессовый цех. Санитарно-гигиенические условия труда в таких цехах характеризуются наличием в воздухе производственного помещения вредных токсичных веществ: масляный аэрозоль, образующийся при смазывании штампа; продукты сгорания смазочных материалов; сернистый газ; сероводород и др. Большие концентрации (3,9-4,1мг/м3) пылевидных частиц, окалины и графита, сдуваемых сжатым воздухом с поверхности матрицы поковок. Существуют выделения токсичных газов от нагревательных печей.
Кузнечно-прессовые цеха характеризуются значительным выделением теплоты, передаваемой излучением и конвекцией. Интенсивность теплового потока у нагревательных печей, прессов, молотов составляет 1,4-2,1кВт/м2; на рабочих местах при нагреве металла на высокочастотных установках 0,24-0,3кВт/м2.
Конечно же, в таких цехах повышенный уровень шума и вибраций.
3. Цех термообработки. Опасные и вредные факторы, возникающие при термической обработке изделий, обусловлены ее видом, применяемым оборудованием и рабочими средами (расплав солей, воздушные, вакуумные и др.)
Основное оборудование – печи, нагревательные и охлаждающие устройства. Дополнительное – правки, очистки, оборудование поверхностного упрочнения, нанесения гальванических покрытий. Вспомогательное – средства механизации, подъемно-транспортное оборудование, вентиляторы, маслоохладительные системы.
Основные вредные и опасные производственные факторы:
1) Повышенная загазованность и запыленность воздуха рабочей зоны. Токсичными газами, содержащимися в составе контролируемых атмосфер и исходных газах, являются: окись углерода, аммиака, диоксид серы, бензол и др. Появление резкого запаха некоторых газов, например аммиака, является предупреждением о неполадках, а именно о нарушении герметичности трубопроводов и оборудования, о внезапном прекращении подачи воздуха в зону горения или об отсутствии устройств для отсоса воздуха от окон и дверей печей. В процессе термической обработки применяются цианистые соли – сильнейшие яды. При обработке растворами образуются выделения, и может происходить их разбрызгивание в результате химических реакций, протекающих на обрабатываемом материале. При этом пары щелочей и мелкие капли водяного пара в сочетании с другими солями могут быть причиной респиративных раздражений, воздействий на слизистую оболочку, органы зрения.
2) Повышенная температура материалов и поверхностей оборудования, повышенный уровень теплового излучения. Ожоги можно получить при выбросах расплава (если нарушен технологический процесс); при возгорании закалочных масел; при воспламенении горючих газов; при прикосновении к частям печей или к наружным частям оборудования. Перегрев и ожоги возможны за счет интенсивного теплового излучения, величина которого без применения средств защиты может достигать следующих значений: при загрузке в закалочно-отпускной агрегат 1,11 – 1,74 кВт/м2, при выгрузке из этого агрегата 0,35 – 0,49 кВт/м2; при подъеме деталей из вертикальной закалочной печи 2,1 – 3,13 кВт/м2; при подогреве в газовой печи с выдвижным подводом 0,35 – 0,7 кВт/м2, учитывая, что допустимая интенсивность теплового потока на постоянных рабочих местах равна 0,14 кВт/м2.
3) Повышенное значение напряжения в электрических цепях. Электротермическое оборудование имеет токоведущие части непосредственно в рабочей зоне, зачастую без электрической изоляции, что представляет опасность при соприкосновении с такими частями в момент загрузки, выгрузки или перемещения нагреваемых изделий. Контакт человека с токоведущей частью возможен также через изделие или инструмент.
4) Повышенная напряженность электромагнитных полей. Электротермические установки для индукционного нагрева металлов и сплавов с машинными ламповыми генераторами относятся к типу электрических установок высокого напряжения (8 – 11 кВ), в которых ток промышленной частоты преобразуется в ток повышенной (0,5 – 10 кГц) или высокой (60 кГц – 5 МГц) частоты. При эксплуатации высокочастотных установок на организм человека могут воздействовать электрические и магнитные поля. При превышении допустимых норм, отсутствии защитных экранов воздействие электромагнитных полей вызывает помутнение хрусталика глаза, которое обнаруживается только через несколько дней или недель.
5) Повышенный уровень шума на рабочих местах и использование ультразвука при очистке и обезжиривании.
6) Движущиеся машины и механизмы (части оборудования, заготовки, материалы и т.д.)
Работы термиста связаны со значительными перемещениями в течение смены (4 – 5 км), переносом тяжестей массой до 10 кг и с неудобной рабочей позой в течение длительного времени.
4. Гальванический цех. Общая система мероприятий по безопасности труда при нанесении гальванических покрытий установлена ГОСТом 12.3.008-75 «Производство покрытий металлических и неметаллических неорганических. Общие требования безопасности». Современная технология нанесения гальванических покрытий состоит из следующих основных технологических операций: подготовка поверхности перед нанесением покрытий, приготовление растворов и электролитов, нанесение покрытий и их обработка.
Подготовка поверхностей. Есть следующие механические методы – шлифование, гидропескоструйный и дробеструйный, струйный с использованием металлической пыли. Эти методы характеризуются повышенной запыленностью металлической пылью, повышенным уровнем шума и вибрации, опасным уровнем напряжения в электрической цепи. Более эффективные и производительные методы подготовки поверхностей это химические, химико-механические, электрофизические, в которых опасными и вредными факторами являются органические растворители и др. химические вещества.
Приготовление электролитов. Вредные факторы это наличие химических веществ, таких как соли никеля, меди, цинка, хрома, цианистый натрий и калий, фенол, формальдегид, различные щелочи и кислоты. Такие вещества приводят к отравлениям и профессиональным заболеваниям. Опасность для человека представляет не только состав электролита, но и режим его работы, т.е. другими словами необходимо строго соблюдать технологические требования к режиму нанесения покрытий с точки зрения безопасности труда, т.к. при нарушении требований (увеличение продолжительности обработки, или увеличении температуры электролита) происходит увеличение испарения электролита. Кроме химических опасных и вредных факторов в гальванических цехах есть физические вредные факторы (шум, вибрации, ультразвук, электрический ток) и пожаро- взрывоопасность.
5. Цех механообработки. При механической обработке металлов, пластмасс и др. материалов на металлорежущих станках возникают:
1) Физические вредные и опасные факторы (движущиеся части оборудования, передвигающиеся изделия, высокая температура поверхностей деталей и инструмента, металлическая стружка, повышенная запыленность и загазованность воздуха, высокий уровень шума, вибрации, недостаточная освещенность);
2) Химические (при обработке полимерных материалов в воздух рабочей зоны поступает сложная смесь паров, газов и аэрозолей, а аэрозоль нефтяных масел , входящих в состав СОЖ может вызвать раздражение слизистых оболочек верхних дыхательных путей, способствовать снижению иммунобиологической реактивности);
3) Психофизические (физические перегрузки при установке, закреплении и съеме крупногабаритных деталей, монотонность труда, перенапряжение зрения);
4) Биологические (болезнетворные микроорганизмы и бактерии, проявляющиеся при работе с СОЖ).
6. Сборочный цех. Из физических факторов наибольшее значение имеют локальная вибрация и шум, создаваемые ручным механизированным инструментом, клепальными машинами, испытательными стендами, вибробункерами сборочных машин и т.д. Источники шума: молоты, прессы, вентиляторы, бункеры и др. При промывке и обезжиривании используется низкочастотный ультразвук (16-44 кГц) высокой интенсивности до 6-7 Вт/см2, а при контроле сборочных соединений – высокочастотный (>80 кГц). Наиболее опасен контактный ультразвук при передаче через жидкости или твердые материалы.
Опасность отравлений возникает при неправильном обращении с органическими растворителями, ароматическими углеводородами, хромосодержащими притирочными и полировальными пастами, различными клеями и герметиками. Наличие металлической и абразивной пыли в воздухе рабочей зоны может привести к заболеванию слесарей-сборщиков хроническим пылевым бронхитом, профессиональной бронхиальной астмой. Применение поточно-конвейерных методов на сборке, чрезмерное дробление трудового процесса, увеличение однообразных движений вызывает состояние монотонности, снижаются функциональные возможности организма, появляется сонливость.
7. Сварочный цех и цех напыления. Повышенная запыленность и загазованность воздуха рабочей зоны, ультрафиолетовое, видимое и инфракрасное излучение сварочной дуги, электромагнитные поля, ионизирующие излучения, шум, ультразвук, статическая нагрузка на руку, содержание в воздухе сварочных аэрозолей (в составе которых металлы никель, хром, титан, алюминий, железо, вольфрам и др.) и токсичных газов (окись углерода, окислы азота и др.), могут быть искры, брызги и выбросы расплавленного металла.
Наиболее распространенным заболеванием работников-плавильщиков является хронический бронхит, т.к. рабочие подвергаются воздействию аэрозолей конденсации 6-ти валентного хрома, широко используемого для получения легирующих добавок для качественных сталей. Рабочий-плавильщик со стажем 28 лет имел токсико-пылевой бронхит – эмфизему легких с дыхательной недостаточностью – профессиональный рак легкого (через 6,5 лет после эмфиземы). Литейщики (рабочие формовочных отделений, обрубки) со стажем работы более 7 лет имеют болезненное состояние верхних дыхательных путей. По статистике у литейщиков с производственным стажем 17 … 18 лет и профессиональным 10 … 11 лет:
– 3,7 % обследованных имеют органические поражения среднего уха воспалительного характера (шум в ушах, ухудшение слуха);
– 11,8 % – повышен порог слухового восприятия на 35 – 40 дБ.
Средний возраст работающих в литейном цехе с симптомами слуховой дисфункции:
– обрубщики 45 ± 4 года;
– формовщики 36,5 ± 3,2 года;
– стерженщики 39 ± 6,2 года.
Виброболезнь обнаруживается через 5 … 8 лет от начала работы на виброопасной профессии, из всех обследованных работников металлообрабатывающей промышленности приблизительно 50 % больных – обрубщики литья и 50 % – формовщики, шлифовщики, слесаря.
Профессиональные заболевания кожи обнаружены у 31,4 % работников металлообрабатывающих специальностей и 5,7 % работников химической специальности. Из всех заболеваний подавляющее большинство 91,8 % составляют аллергические дарматиты и большой процент 86,8 – поражения кожи именно открытых частей тела.
У слесарей-сборщиков (уровень шума на рабочем месте превышал ПДВ на 5 – 10 дБ, максимальные уровни виброскорости на частотах 125 – 250 Гц): в возрасте до 40 лет со стажем работы от 5 лет жалуются на усталость в руках к концу смены, боли в предплечьх, суставах, судороги в пальцах; у 20,1 % – заболевания опорно-двигательного аппарата, причем чем больше стаж, тем больше жалоб. У слесарей-ремонтников (работа сходная, только без вибрации и шума) процент заболеваемости значительно ниже (6,6), причем зависимости от профессионального стажа не выявлено.
У рабочих занятых на кислородной резке металлов (содержание в воздухе окислов железа, марганца, азота, окись углерода превышает ПДК) появляются хронические профессиональные заболевания – пылевой бронхит и по типу острых отравлений (металлическая лихорадка, отек легких, токсическая пневмония). Из обследованных острой пневмонией в возрасте 15 … 36 лет: 24 % больных – работники умственного труда; 76 % – работники физического труда, причем мужчины болели чаще, чем женщины из-за вредных привычек.
В кузнечно-прессовых цехах и термических участках из-за повышенной температуры окружающего воздуха и значительного теплового (инфракрасного) излучения у рабочих возникает перегрев (или более тяжелая форма – тепловой удар) и судорожная болезнь.